EDM Machining
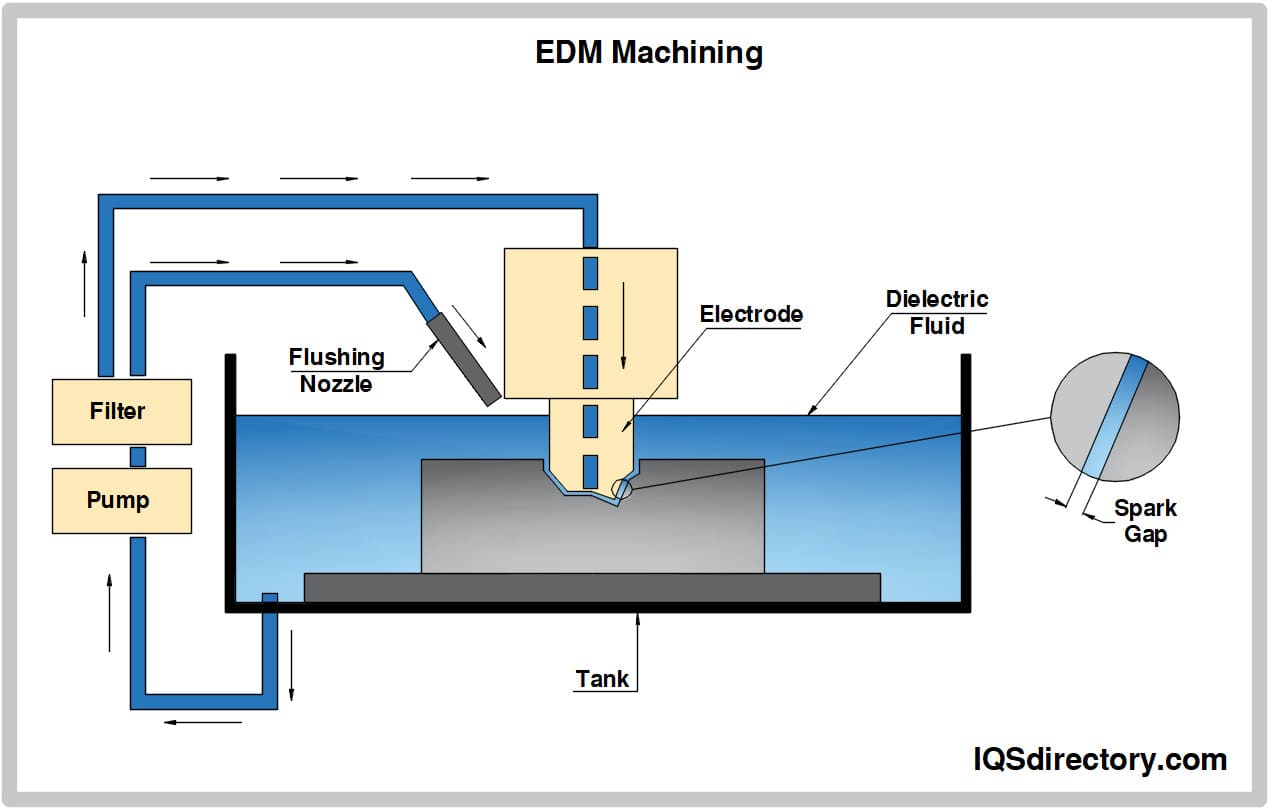
EDM machining is a contemporary machining method based on the removal of material from a part using thermal energy. The material is removed by local melting or vaporizing small areas on the surface of the part being machined...
Please fill out the following form to submit a Request for Quote to any of the following companies listed on
This article contains everything you need to know about sinker EDMs and their use.
You will learn.
Sinker Electrical Discharge Machining (EDM) is a technique used in metalworking to craft molds, dies, and intricate components through the erosion of material using electrical discharges. This method is favored for its capability to achieve complex geometries with exceptional precision and consistency compared to other machining processes.
The term "sinker EDM" derives from the method's ability to "sink" into the material as it erodes it. Sometimes called "burning," this process generates tiny craters to sculpt and shape the workpiece. For sinker EDM to be effective, the workpiece must be made of electrically conductive material or a ferrous alloy.
Manufacturers favor the sinker EDM process because it can precisely cut extremely small components with remarkable accuracy. This technique is especially useful for creating intricate parts that would be difficult to achieve with other methods. Sinker EDM is also employed to create prototypes for client review and to refine designs for alternative manufacturing processes.
The first step in the Sinker EDM process is to design the electrode. The electrode is typically made of copper or graphite and is shaped to match the desired shape of the workpiece. The electrode is mounted on the machine's electrode holder and connected to the power supply. The choice of electrode design has a major impact on the number of electrodes needed, the rate of metal removal, the surface finish, and the running stability. To enhance the efficiency of the process, multiple electrodes can be used with each electrode creating its own spark and only one electrode sparking at any one time.
Electrode design involves selecting the appropriate type of electrode, such as staged, pieced, or partial area electrodes. These types vary based on the number of electrodes, the materials used in their construction, and their cutting capabilities.
In the EDM process, dielectric fluid serves as both a coolant and an electrical insulator. This fluid circulates around the electrode and the workpiece to prevent arcing and to wash away the eroded material. It also helps regulate the temperature at the machining site, reducing the risk of thermal expansion.
Dielectric fluids are typically composed of petroleum-based liquids or synthetic oils, although some water-based options are available. These fluids are designed to offer high electrical resistance and low viscosity, enabling effective insulation of the electrical discharge and smooth flow around the workpiece. Certain dielectric fluids include additives to enhance their cooling and lubricating properties.
The dielectric fluid is essential in the sinker EDM process, as it removes particles of burnt metal and electrode material from the machining area, directing them into the filtration system.
To ensure the success of the sinker EDM process, specific requirements for the workpiece must be met. The material used must be electrically conductive, though it does not necessarily need to be machinable. Proper preparation of the workpiece is crucial, which includes thorough cleaning to remove contaminants such as dust, particles, and other debris. Any residual materials can disrupt the interaction between the workpiece and the electrode, potentially causing damage to the electrode and reducing the efficiency of the process.
The initial step in preparing the workpiece involves immersing it in deionized water or a non-conductive lubricant. This helps remove the molten material that is cut from the workpiece and separates it from the electrode. The fluid is kept in continuous motion to cool the removed particles and to keep them away from the electrode and workpiece. Additionally, the deionized water or lubricant aids in managing the electrical discharge between the workpiece and the electrode.
Throughout the sinker EDM process, maintaining the purity of the fluid is essential for process success. The temperature of the fluid is also closely monitored to ensure it remains constant and stable, which is vital for consistent results.
The electrode is carefully aligned above the workpiece, ensuring that a voltage gap exists between them for electrical discharge. It is crucial that the electrode does not make contact with the workpiece, as this could result in welding the electrode to the workpiece, causing damage to both. When positioned correctly, the heat generated by the discharge vaporizes minute particles from the workpiece, which are then carried away by the dielectric fluid flow.
During the sinker EDM machining process, the electrode must be positioned so that it remains at a safe distance from the workpiece. This distance allows the spark to melt material without physical contact. This method eliminates the need for cutting pressure, which is a distinctive feature of sinker EDM.
Since the electrode plays a critical role in the sinker EDM process, its positioning within the dielectric fluid is precise and closely controlled relative to the workpiece. The electrode, typically made of materials like copper or graphite, is shaped in reverse of the features it will create. The positioning process is meticulous and continues until the electric breakdown occurs, allowing sparks to jump across the gap.
The power supply delivers a high-voltage electrical discharge between the electrode and the workpiece, creating a spark that erodes the material of the workpiece in accordance with the electrode's shape. As the electrode approaches the workpiece, sparks leap across the gap, generating temperatures ranging from 8000°C to 12000°C (14,432°F to 21,632°F). These extreme temperatures erode the metal, forming it to match the electrode's geometry.
The energy of the sparks is influenced by the combination of amperage, voltage, and pulse duration. Each spark pulse increases the electrical current until it reaches the predefined level. For this to occur, the gap voltage must establish an ionization path. Once the current starts to flow, the voltage drops to a stable operating level, which is controlled by the sinker EDM settings and dictates the width of the spark gap between the workpiece and the electrode. An increase in voltage results in a wider gap.
Higher amperage and longer pulse durations produce more heat with each discharge from the electrode. This results in a faster burn rate and the removal of larger metal particles, known as swarf. The presence of swarf can cause repeated sparking in the same area, potentially damaging the workpiece and affecting its finish.
The spark's behavior is regulated by adjusting parameters such as pulse duration and current on the power supply. This ensures that material is eroded in a controlled fashion, removing tiny particles. The dielectric fluid continuously circulates around the machining zone to clear away eroded material and prevent arcing, which is crucial for managing the effects of swarf.
Originally, sinker EDM operations were manually overseen by operators who monitored the process and made necessary adjustments in response to any issues. With the rise of CNC machining and the need for faster manufacturing, adaptive monitoring and control systems have been introduced. These systems analyze the spark conditions and convert these readings into digital signals, which are then interpreted by the EDM machine’s controller.
To address issues like swarf accumulation in the voltage gap, the monitoring system detects contaminants and adjusts parameters without compromising the quality of the workpiece’s surface. Adjustments may include modifying gap voltage, extending off-time, and altering the discharge cycle to mitigate the effects of contamination.
The adaptive controller oversees the process, activating and deactivating as necessary based on factors such as electrode size, material removal rate, contamination levels, and the desired surface finish. It continuously adjusts the machining settings to maintain a smooth operation.
This control system manages a comprehensive set of parameters to regulate the sinker EDM process. It quickly adapts to changes without requiring manual adjustments and is capable of handling a broad range of production needs.
Sinker EDM yields exceptionally smooth and uniform mirror-like surfaces. Depending on the specific parameters of the part being fabricated, additional finishing processes might be necessary. These finishing steps are crucial for improving both the appearance and durability of the part, ensuring that it meets the design requirements and specifications.
Sinker EDM is capable of machining even the hardest and most challenging metals, provided they are conductive. This technique produces minimal distortion and eliminates residual stress. The origins of EDM trace back to 1943, when submerged electrodes in a dielectric fluid enabled precise erosion control. This method was developed as a more effective alternative to etching tools, which lacked the power needed for cutting through metals.
Small hole EDM employs a tiny, hollow, rotating brass electrode to shape the workpiece. While this process resembles drilling, it benefits from the precision of EDM machining. Often referred to as EDM drilling or EDM micro hole drilling, this technique requires minimal force and is perfect for creating intricate, delicate components with high precision.
As with all forms of EDM processes, small hole EDM machining can be used on any ferrous metal regardless of its hardness. The brass tube channels electricity to make different size holes. Small hole EDMs are used to place minute holes in the workpiece, even when the workpiece has inclined faces or difficult to reach positions.
Traditional Sinker EDM, also known as die sinking EDM, utilizes an electrode crafted from copper or graphite, designed to match the profile of the part being produced. When activated, the electrode is submerged in dielectric fluid, where electrical sparks erode the material from the workpiece to achieve the desired shape.
This conventional sinker EDM technique offers high precision, allowing for the accurate reproduction of detailed parts with tolerances as tight as +/- 0.0003 inch. Its exceptional precision makes it a preferred choice for producing prototypes and intricate small components.
Orbital Sinker EDM represents an advanced version of traditional sinker EDM, utilizing a specially engineered electrode that rotates and orbits around the workpiece during the machining process. This method enhances the discharge area and minimizes electrode wear, resulting in quicker and more precise machining.
This technique is effective for both roughing and finishing operations, reducing the need for subsequent polishing. The orbital head of the machine moves the electrode around the central axis of the workpiece, allowing for greater control over the precision of the cuts. The burn size is adjusted based on the electrode's dimensions, eliminating the need for multiple electrodes to achieve the same results.
Orbital Sinker EDM improves surface conditions and prevents tapering on cavity walls. The process can be finely tuned to achieve exact hole sizes, and the orbiting motion facilitates Z-axis burns to specified depths, effectively removing tapers caused by secondary discharges. Additionally, the orbital movement creates a vacuum effect that draws more dielectric fluid into the gap, expelling particles and leading to a cleaner finish.
Ram EDM produces its spark along a formed electrode instead of a wire. A servo system prevents the ram electrode from touching the workpiece. The process has the same capabilities as wire sinker EDM and is able to form parts with exceptional precision and intricacy. Ram EDM allows for a wider range of machining operations, including the production of more complex shapes and features.
Wire EDM and small hole EDM techniques focus on removing material along a precise line or from a single point. In contrast, Ram EDM enables the creation of three-dimensional shapes by using an electrode that is a negative replica of the final part. For Ram EDM, electrodes are typically CNC machined to achieve this negative image. These electrodes, often crafted from brass, are suitable for machining tough materials such as tungsten carbide and Inconel.
Multiple electrode sinker EDM allows for simultaneous machining of several areas on a workpiece, with each area achieving consistent shape, accuracy, and finish. This approach accelerates the process, reducing setup time and energy consumption, though it may sometimes result in slight inaccuracies and rougher finishes.
Employing multiple electrodes in sinker EDM enhances both efficiency and precision. The increased number of channels facilitates improved debris removal and cooling, which accelerates the cutting process and reduces electrode wear. This method is particularly effective for complex and precision applications, yielding high-quality finishes.
The advancement of multiple electrode sinker EDM addresses the need for higher material removal rates, superior surface finishes, and reduced energy usage. By machining multiple areas concurrently, this technique significantly shortens processing time and accelerates rough machining, despite the initial setup requirements.
Pulse Power Sinker EDM utilizes advanced pulse generators to extend the duration of discharge energy, enhancing both machining accuracy and surface finish. This technique is particularly beneficial for working with materials that are challenging to machine using traditional Sinker EDM methods.
By prolonging the pulse duration, Pulse Power Sinker EDM removes more material from the workpiece. This results in larger and deeper holes compared to those produced with shorter pulses. Additionally, the extended pulse allows for greater heat penetration into the workpiece, affecting a broader and deeper area.
Different types of Sinker EDM offer various benefits and limitations. Choosing the most suitable process depends on the specific requirements of the application and the outcomes desired. Metalworking manufacturers can offer valuable guidance and expertise in selecting the optimal EDM process for your needs.
The sinker EDM process is particularly effective for drilling holes into hardened materials. For creating holes, a small pilot hole can be initially drilled into the workpiece, through which a wire EDM can then be inserted to complete the hole formation. However, for blind holes or larger diameters, this method is insufficient, and a specialized tool known as a “hole popper” is required.
In this method, a continuous stream of dielectric fluid is used alongside a rotating conductive tube to drill large holes. The dielectric fluid effectively flushes away the material as it is removed, ensuring precise and accurate hole creation even in the hardest materials.
The wire EDM was perfected in the 1960s as a method for making dies from hardened steel. The process uses a thin wire that moves in a controlled pattern like a woodworker’s scroll saw. As the wire continuously moves and erodes the workpiece, wire from a spool is fed into the discharge area to be able to provide a fresh discharge path.
The “cheese cutter” technique involves making a two-dimensional cut through a three-dimensional workpiece. In contemporary sinker EDM machines, the wire's movement across the XY plane is controlled via CNC programming, allowing for precise and automated cuts.
One of the key advantages of EDM machines is their ability to work with any conductive material, enabling the creation of intricate depths and shapes that are challenging to achieve with other cutting techniques. When choosing an EDM machine, it's essential to consider factors such as the design requirements and specific application needs.
EDM machines are renowned for their ability to make highly precise cuts in conductive materials. The optimal sinker EDM machine for a project is selected based on factors such as the material type, the precision needed, and the finish quality required. These machines are particularly effective for creating blind holes and complex cavities in molds and dies.
The Mitsubishi MX600 represents the forefront of sinker EDM technology. It features a granite base designed to stabilize the workpiece and minimize floating capacitance. The MX600's advanced nano-FS circuit enhances cutting speed and achieves exceptionally fine surface finishes, with precision as low as 1.4 µm, all without the need for specialized tooling. One of its standout features is the automatic wire feed system, capable of handling wires as thin as 0.0008 inch (0.02032 mm).
Additionally, the dielectric oil used in the MX600 helps prevent cobalt depletion during carbide machining and avoids rusting in iron-based machining. The machine is equipped with linear guideways and extended linear guide bearings to reduce guide waviness, ensuring smooth operation.
ONA offers a diverse range of sinker EDM machines tailored to various manufacturing requirements. The ONA IRIS T7, for example, boosts production efficiency by 200% and cuts erosion time by 50%, while accommodating workpieces up to 28 tons (25,000 kg). This machine features a robust three-axis system with an enhanced C axis for improved stability during erosion. Additionally, its user-friendly touch screen interface simplifies the programming process, making it both quick and efficient.
Makino sinker EDM machines feature a large touch screen interface designed for intuitive use, similar to a smartphone, enabling operators of varying skill levels to manage the machine with minimal training. Enhancements in flushing and debris removal have significantly increased the erosion rate, with a Z-axis jump rate that's four times faster and an acceleration rate 30 times quicker than earlier models. These improvements not only reduce electrode usage and operational costs but also deliver more consistent finishes.
Fanuc's EDM wire machines are branded as Robocut, covering a range of models designed for cutting small, medium, large, and versatile parts. Robocut machines are equipped with a factory-calibrated grid for worktable pitch correction. They also feature automatic wire threading software that can rethread wire in just ten seconds. Notable elements of the Robocut design include an advanced user interface and an economy mode that enhances energy efficiency and reduces wire consumption.
Sodick's sinker EDM machines are known for their vibration-free operation and zero backlash, thanks to their linear motor technology. This ensures high cutting precision and exceptionally smooth finishes. Sodick offers a range of sinker EDM models with varying XYZ travel ranges, from just over a foot to several feet. Key technologies in Sodick sinker EDMs include the power supply unit, discharge unit, linear motor, motion controllers, and advanced ceramic components.
Choosing the right material is crucial in sinker EDM, as it significantly affects the effectiveness and results of the machining process. Key considerations include the material’s electrical conductivity, which is essential for achieving optimal shaping and erosion. Evaluating the material's properties ensures that the sinker EDM process performs efficiently and meets the desired outcomes.
Sinker EDM requires materials with electrical conductivity for effective operation. Metals are ideal for this process, as they allow for the smooth flow of electricity necessary to generate the electrical discharge. While untreated ceramics and plastics are non-conductive and unsuitable for sinker EDM, some ceramics and plastics can be processed if they are combined with conductive metals. The key to successful sinker EDM is ensuring that the workpiece completes the electrical circuit by being sufficiently conductive.
Conductive materials, including various metals and graphite, can be machined using sinker EDM. Graphite, although non-conductive itself, is used to produce electrodes. While pure ceramics and plastics are not suitable for sinker EDM, adding conductive metals to these materials can make them viable for the process. The core requirement of sinker EDM is that the workpiece must complete an electrical circuit, which necessitates the use of conductive materials.
The melting point of a metal plays a crucial role in determining the energy required for the sinker EDM process and influences the erosion rate. Metals with higher melting points demand more energy and longer processing times. While the hardness of the metal does not directly impact the sinker EDM process, the thermal properties of the metal, including its melting point, significantly affect machinability. Metals vary widely in their melting points based on their composition and purity, which are essential factors in material selection for sinker EDM.
The metal's melting temperature influences the performance of the sinker EDM machine, as it impacts the metal removal rate (MRR). This rate is governed by the metal's melting point and thermal conductivity. Tungsten carbide, for example, has a notably high melting point, which affects its machining characteristics.
The melting point of a metal affects not only the efficiency of the EDM process but also the types of equipment required. Metals with higher melting points necessitate more robust machinery and greater energy consumption. Additionally, the melting point is crucial in determining the rate of material removal and the wear on electrodes during the EDM process.
Melting Point of Various Workable Metals | ||
---|---|---|
Metal | F° Melting Point | C° Melting Point |
Aluminum (6061-T6) | 1080° - 1200° | 582° - 649° |
Inconel (718) | 2300° - 2437° | 1260° - 1336° |
Stainless Steel (410) | 2700° - 2790° | 1482° - 1532° |
Tool Steel (06) | 2732° | 1500° |
Titanium (Ti-6AL-4V) | 3000° | 1649° |
Tungsten Carbide (K-68) | 6054° | 3360° |
Machinability refers to how easily a metal can be shaped and cut. Metals that are easily machinable require less energy to cut and can be deformed more readily to achieve the desired shape. These metals typically produce better parts with tighter tolerances and exceptional surface finishes. They are processed more quickly, cause less wear on tools, and lead to longer tool life, resulting in cost savings and better use of machine shop resources.
In the sinker EDM process, there is a trade-off between the machinability of metals and their strength. Each design specifies certain parameters and materials, requiring designers to balance the choice of metal with the amount of machining required to achieve the final product. Harder metals with low machinability take longer to process and shape, often resulting in increased tool wear and the need for frequent adjustments.
For applications like die manufacturing, where the metals are very dense and hard, significant energy is required for processing. These metals must be exceptionally hard due to the demanding nature of their function. In such cases, the sinker EDM process is advantageous as it can handle these hard metals and produce components with fine details and tight tolerances, despite the low machinability of the materials.
The surface finishes produced by sinker EDM are distinct from those achieved with other material removal processes. The texture is random, and multiple passes create a nearly mirror-like quality. This is particularly important in applications where parts slide over one another, as the micron-sized holes produced by sinker EDM differ from the directional lay left by cutting tools.
To achieve the most accurate finish, most parts require multiple passes. The process typically starts with a rough cut to remove the bulk material, followed by a finish cut that refines the part's geometry. The final pass, known as the surface finish cut, is exceptionally fine and produces a very smooth surface.
Since sinker EDM can process any form of metal, the desired surface parameters are determined during the initial planning phase, including the selection of the appropriate metal. The choice of metal affects the time required to achieve the finish, as some metals necessitate more processing.
One of the key advantages of sinker EDM is its ability to produce high-quality finishes with minimal need for secondary processing. The process is not affected by material hardness, simplifying the selection of metals for various applications.
The key criterion for using sinker EDM is that the metal must be electrically conductive, which generally limits choices to ferrous metals and aluminum. While copper is highly conductive and might seem like an ideal choice, it is not always preferred for sinker EDM machining. This is because the process heats copper rapidly, necessitating constant temperature control and adjustments to avoid complications.
All forms of steel can be machined using the sinker EDM process due to their toughness, strength, durability, and resilience. Alloy steels, in particular, have elements added to enhance their properties, including chromium, cobalt, columbium, molybdenum, manganese, nickel, titanium, tungsten, silicon, and vanadium. These various alloys modify the properties of steel, adding desirable characteristics for different applications.
Copper is an excellent choice for the sinker EDM process due to its high conductivity. However, its use can be challenging because copper heats up quickly and transfers heat through the metal, necessitating careful control and a slower process. Despite these challenges, sinker EDM can effectively work with copper components, including those with thin walls, without causing warping or distortion.
Tungsten carbide is a challenging material to machine due to its high hardness, high melting point, and brittleness. Sinker EDM is well-suited for machining tungsten carbide because it effectively manages the differential heat conduction caused by its unique structure.
Electrodes for tungsten carbide are made of copper using negative electrode polarity, which produces very low surface roughness. When machining tungsten carbide, using sinker EDM, the removal rate is very slow due to the nature of the metal. Small intricate and complex geometries can be produced using the process.
Titanium is renowned for its exceptional strength-to-weight ratio, corrosion resistance, and ability to withstand high temperatures. Its biocompatibility makes it a popular choice for medical implants. However, the high hardness of titanium poses challenges for conventional machining methods. Similar to tungsten carbide, titanium is effectively machined using sinker EDM with copper electrodes and carefully controlled pulse on and off times.
Nickel can form alloys with a variety of metals, such as chromium, iron, molybdenum, and copper. These diverse combinations enable nickel to exhibit a range of properties, including resistance to corrosion, high-temperature endurance, exceptional strength, shape memory, and low thermal expansion. Nickel alloys can be created with individual metals or in combinations like nickel-chromium-molybdenum or nickel-chromium-cobalt.
Nickel alloys are often employed in demanding environments because of their ability to perform reliably under extreme conditions. Despite their remarkable strength, these alloys remain malleable and do not become brittle, unlike iron, which can be brittle, or copper, which is soft and ductile. When alloyed with nickel, both iron and copper gain enhanced strength, durability, and resilience. For instance, alloys combining copper and nickel can have a lifespan exceeding thirty years.
One of the notable features of nickel is its high melting point, approximately 1455°C (2651°F), which contributes to its stability at elevated temperatures. Nickel's low density, along with its controlled thermal expansion and thermal conductivity, further underscores its effectiveness as a material resistant to heat.
Aluminum is a widely available metal utilized in a diverse range of applications and products. Its inherent resistance to oxidation, corrosion, and rust contributes to its durability. Aluminum is rarely used in its pure state and is usually alloyed with other metals to enhance its properties. Its suitability for sinker EDM work is due to its capacity to be molded into detailed and complex forms.
The metals mentioned above represent just a fraction of those that can be processed using sinker EDM machining. Essentially, any conductive metal can be shaped and machined with this technique. The choice of the most suitable metal for a particular application is typically determined by both the manufacturer and the customer.
The sinker EDM process comprises several key components: the worktable, electrode, tank, dielectric fluid, servo control system, control panel, filtration system, and power supply. At the heart of the process is the workpiece, which must be made from a conductive metal to enable the completion of an electrical circuit. The dielectric fluid used is either deionized water or a non-conductive lubricating oil. These elements collaboratively function to shape and form the workpiece, resulting in the final product.
The worktable of a sinker EDM machine is crucial for securely holding the workpiece throughout the machining process. It allows movement along the X, Y, and Z axes for accurate positioning, with some models also offering adjustments along the A and B axes. Worktables vary in design to meet different EDM machine needs, featuring multiple axis settings and construction that resists dielectric fluids like water or oils. The internal components of the worktable are insulated from the electrical currents used during the machining process.
The five-axis configuration of many sinker EDM worktables enables highly precise cuts with tight tolerances. This design allows for the continuous rotation of the workpiece while keeping the electrode stationary. Proper electrode positioning is critical to ensure it maintains the correct distance from the workpiece, providing an adequate discharge gap and optimizing the machining process.
The tank in a sinker EDM setup is designed to hold the dielectric fluid, which may be deionized water or non-conductive oil. This robust container is crucial for the EDM process, as it houses the dielectric fluid, worktable, workpiece, and electrodes. The tank's primary function is to provide a stable environment for the machining process, containing all essential components in one location.
One key function of the tank is managing the flow of the dielectric fluid to ensure that particles from the cutting process are effectively removed from both the electrode and the workpiece. While all tanks are designed to maintain fluid flow, some models include specialized mechanisms to enhance this flow rate.
Due to the neutral and non-acidic nature of dielectric fluids, there is minimal risk of tank damage from the fluid itself. However, it is crucial that the tank is well-sealed to prevent leaks, which could disrupt the process. Many tanks are connected to a dielectric fluid reservoir system that allows for the fluid to be continuously filtered and recirculated, maintaining its purity and ensuring effective flow throughout the process.
The quality of the workpiece surface in sinker EDM is largely influenced by the control of the electrode arc. This control involves maintaining a consistent power and energy supply from the power source, which provides the necessary current and voltage to generate the arc. While the power supply manages the current electronically, the voltage across the arc is influenced by the gap distance, which is adjusted mechanically. The integration of these electronic and mechanical controls is known as the EDM servo motor system.
The power supply regulates the duration of the arcs, which can range from 1 microsecond to 250 microseconds. Because sinker EDM processes are relatively slow, shorter pulse durations are generally preferred, with arc frequencies often reaching tens of kHz to enhance machining efficiency.
The power supply must set the voltage high enough to initiate the sparking process, typically over 100V, but not excessively high. It controls the pulse speed, current, and arc duration. In some systems, reversing the polarity between the workpiece and the electrode can be done electronically, reducing the need for manual adjustments during the process.
The electrode, crafted from conductive materials like copper or graphite, is a precisely shaped tool that helps form the desired contours in the workpiece. It is linked to the power supply and, at the start of the process, is submerged along with the workpiece into the dielectric fluid within the tank. Through a non-contact sparking mechanism, the electrode erodes material from the workpiece to achieve the intended shape.
The servo control system manages the movement of the electrode, worktable, and the spark discharge gap. Equipped with a gap sensor, it measures the voltage of each machining pulse. The system's precision motor and feedback sensors ensure accurate electrode movement in both direction and speed. It also determines the optimal spacing between the electrical discharge electrode and the workpiece to ensure precise machining.
The filtration system is designed to clear debris and particles from the dielectric fluid, maintaining a clean and efficient machining environment. During the sinker EDM process, sparks generate tiny cavities in the workpiece, producing waste material that could disrupt the process. The filtration system effectively captures and removes this waste material to prevent interference.
The control panel serves as the operator’s interface with the machine, enabling them to set machining parameters and track the progress of the operation.
Every component of a sinker EDM machine plays a crucial role in ensuring the performance and precision of the process. Manufacturers offer guidance and training to help users effectively operate these machines and tailor the equipment to meet specific customer needs.
In addition to basic linear cutting sinker EDM machines, there are multi-axis models that can add complex shapes and tapers to the top, bottom, and sides of a workpiece. These advanced machines enhance production speed and efficiency by allowing for more intricate and varied machining operations.
High-speed sinker EDM machining accelerates the process by enhancing the rate of flushing and debris removal, utilizing a faster Z-axis cycle rate. As traditional EDM machining is typically slow, any method that increases speed helps align EDM with contemporary manufacturing practices. High-speed sinker EDM now competes effectively with conventional milling techniques by offering improved efficiency.
One significant advancement in high-speed sinker EDM is the incorporation of automatic tool changers, which allow machines to operate without manual intervention by changing electrodes every 30 seconds. Additionally, upgrades to the sinker EDM tanks facilitate faster drainage of dielectric fluid, thereby reducing cycle times.
Modern high-speed sinker EDM machines are equipped with cutting-edge technologies, including high-frequency generators, sophisticated servo systems, and high-speed spindles, to enhance machining speed and precision. These innovations aim to broaden the acceptance of sinker EDM across various manufacturing sectors.
The key to improving sinker EDM machining is speed. Although these advancements might suggest potential trade-offs in other areas, high-speed sinker EDM maintains the precision and accuracy that have made it a favored choice among manufacturers.
Traditional sinker EDM machining typically employs a three-axis approach for shaping the workpiece, offering a method that achieves high precision and accuracy in cuts. The introduction of a fourth axis enhances the movement capabilities of the electrode, enabling a broader range of cuts and reducing cycle times.
The standard three-axis sinker EDM machining is limited to linear movements, which can restrict the electrode's cutting capabilities. The addition of a fourth axis introduces rotational movement, allowing the workpiece to be machined along the B axis. This feature is similar to those found in computer numerical control (CNC) machining, contributing to the effectiveness of CNC processes. As sinker EDM technology evolves, it increasingly integrates with CNC methods.
The inclusion of a fourth axis in four-axis sinker EDM machines builds upon the three-axis motion control, enabling more intricate and precise machining tasks. This additional axis allows for better control of the electrode’s angle and position, facilitating the creation of complex shapes and detailed designs. The capability to reposition the electrode for multiple cuts within a pattern is a significant advantage of this advanced axis control.
Five-axis sinker EDM machines extend the movement capabilities of the electrode even further than their four-axis counterparts, enabling the creation of more intricate designs. This additional axis contributes to faster processing speeds and reduced cycle times by allowing more complex machining operations.
While four-axis sinker EDMs introduce rotational movement, five-axis machines take this a step further by enabling the workpiece to be rotated and shaped on all its sides. This means features can be added to the top of the workpiece without needing to pause machining for repositioning, as both the electrode and worktable accommodate the extra motion required.
Overall, the five-axis capability enhances EDM machining efficiency and speed, which is crucial for its broader adoption. Most CNC machines are designed with five-axis capabilities from the outset, making it easier to integrate these features into sinker EDM processes and align them with CNC machining standards.
Automated sinker EDM machines represent a sophisticated evolution in EDM technology, incorporating robotic systems to enhance the process. These machines feature articulated robots, which have multiple joints for performing various movements, to handle tasks such as adding and removing electrodes and workpieces, as well as arranging their layout. The robot's size is tailored to accommodate the weight and configuration of the workpieces being machined.
The integration of robotics and automation has significantly advanced sinker EDM capabilities, enabling the production of more complex and consistent components in larger quantities. Precision control offered by these systems minimizes human error and enhances part quality, allowing for higher production volumes without compromising the quality of the parts.
Automated sinker EDM systems facilitate faster offline setup and boost the accuracy and efficiency of the machining process. The system includes control over the dielectric tank, which must be adjusted to meet the system's requirements. A key advantage of automated sinker EDM is its ability to automate electrode and parts changing, leading to reduced costs and increased productivity over time.
Automated sinker EDM processes are computer-programmed, which enhances repeatability and shortens lead times. Once a process is validated, it can be easily replicated without further system adjustments. This leads to improved part quality, lower labor costs, and increased profitability.
Overall, automated sinker EDM machines contribute to greater process efficiency and speed. Every stage of machining, from initiation to the final product, is meticulously controlled and programmed to ensure optimal performance.
Micro sinker EDM machines are engineered to manufacture extremely small and precise components. These machines utilize cutting-edge technologies, such as ultra-fine wire and high-precision servo systems, to achieve exceptional accuracy and surface finish. Micro sinker EDM processes can make cuts at the micron (µ) level, which is one millionth of a meter, or micrometer.
Specialized for intricate tasks, micro sinker EDM can create features as small as 10 µm (0.0004 inch). The electrodes used in this process are also minuscule, designed to cut tiny holes, slots, and shapes with precision.
Sinker EDM is often used in conjunction with CNC machining when precise, small features are required in delicate areas of a component. In this setup, wire is continuously fed into the dielectric fluid, and its movement is controlled by upper and lower diamond guides, which receive instructions from the CNC machine controller. The multi-axis capability of CNC sinker EDM allows for the programming of complex, precise cuts, making it ideal for creating intricate and delicate shapes.
The enhanced capabilities of sinker EDM machining is further improved with the technology of a CNC machine. The choice of sinker EDM technology with CNC machines is due to the inability of CNC milling and cutting tools to make the highly precise cuts available with a sinker EDM.
Like all industrial equipment, sinker EDM machines are governed by various regulations and standards. In the United States, their use is regulated by agencies such as the Occupational Safety and Health Administration (OSHA), the National Fire Protection Association (NFPA), and the Environmental Protection Agency (EPA). Additional regulations may be imposed by state and local authorities, as well as international organizations.
A primary concern with sinker EDM processing is the generation of toxic and hazardous fumes and materials, which requires stringent oversight and control measures. Regulations mandate specific safety protocols to protect workers and the manufacturing environment, including the use of proper filters and ventilation systems. Furthermore, operators must adhere to protective measures outlined in the machine’s safety manual, which includes wearing appropriate protective gear as specified by the manufacturer.
OSHA enforces several regulations relevant to sinker EDM machines and their operators. For instance, OSHA's General Industry Standard 1910.212 mandates that machinery and equipment be properly guarded to protect workers from potential hazards, including moving parts, electrical risks, and flying debris.
The NFPA provides a set of standards for the use of sinker EDM machines in manufacturing settings. These standards cover essential aspects such as electrical safety, fire prevention, and the handling of hazardous materials to ensure a safe working environment.
The EPA oversees the disposal of waste materials produced by the sinker EDM process. This includes regulations for managing spent electrode materials, used cutting fluids, and other waste products to ensure environmentally responsible disposal practices.
State and local governments may impose their own regulations on the use of sinker EDM machines. These can include requirements for permits or licenses to operate the equipment, as well as specific regulations concerning the disposal of hazardous waste materials.
The International Organization for Standardization (ISO) is a globally recognized entity that sets standards for various manufacturing processes. EDM machining is addressed under ISO 28881:2022, which covers machine tools, safety, and electro discharge machines. Given that many sinker EDM machines are produced outside the United States, both manufacturers and users are diligent in adhering to ISO standards to ensure the safety of their products and the protection of workers.
ANSI standard B11.27-2020 specifies the requirements for electro discharge machines, including safety protocols and risk reduction measures. This standard applies to all types of die sinking, drilling, CNC sinking, and wire cutting machines. Unlike ISO standards, which are primarily focused on manufacturer requirements, ANSI B11.27 provides guidelines for both suppliers and users. This standard is reviewed and updated annually to keep pace with the increasing use of sinker EDM machines.
The sinker EDM process is particularly suited for crafting small, intricate components with exceptional precision. Sinker EDM machines can be programmed to create a wide range of complex shapes from any conductive metal, greatly enhancing the capabilities of parts manufacturers and producers.
Sinker EDM is valued for its ability to produce complex and detailed parts that other manufacturing methods may not achieve. It excels in shaping hard and challenging metals, ensuring that molds and dies meet exact specifications and tolerances for high-quality components.
The versatility of sinker EDM is evident in its ability to shape any type of conductive metal, regardless of its density or hardness. This flexibility makes sinker EDM a preferred method for machining metals that are challenging or impossible to process with traditional techniques.
The range of configurations, forms, and shapes achievable with sinker EDM is virtually limitless, encompassing even the most intricate and complex designs crafted from some of the toughest metals. It is particularly valuable for producing dies and molds that require the highest levels of precision and tolerance in component manufacturing.
The sinker EDM process is renowned for its consistent accuracy, ensuring that every part, regardless of its complexity, is produced with a smooth finish and precise tolerances. The EDM process excels in meeting design specifications due to its programmable nature and the minimal stress it places on the workpiece.
This consistency contributes significantly to the repeatability of sinker EDM machining. Once the parameters for a workpiece are set in a sinker EDM machine, it follows these instructions meticulously, producing identical parts with exact dimensions and specifications. The level of precision and detail achieved with sinker EDM is challenging to replicate with other machining processes.
Traditional milling and cutting processes involve sharp tools that scrape and shape the workpiece by making direct contact with its surface. These tools, typically made from hardened metals, are designed to cut deeply into the material. Despite their robust design, these tools experience wear over time and need to be replaced periodically.
In contrast, sinker EDM utilizes an electrode to shape the workpiece through electrical sparking rather than physical contact. The electrode, often made of graphite or copper, emits electrical sparks that vaporize small particles from the workpiece to form the desired shape. Unlike cutting tools, the electrode in sinker EDM does not physically wear out during the process, though it is subject to electrical wear. Despite the initial cost of manufacturing the electrode, it continues to perform effectively until it needs replacement.
Since sinker EDM does not physically cut into the workpiece, it avoids inducing stress. The process operates on the principle that the workpiece is shaped and formed without the residual stress associated with mechanical methods like bending, drawing, rolling, or cutting.
Performed in a dielectric fluid, sinker EDM employs a tool that does not directly contact the workpiece, thereby eliminating the risk of stress caused by uneven deformation. The electrodes in sinker EDM shape and cut the metal under controlled conditions, allowing for precise and uniform results where the tool and workpiece interact to achieve the desired design.
The outcome of the sinker EDM process is parts that maintain stability and do not warp or alter their shape during use. This is particularly important for applications where precision and stability are critical in assemblies, as the process avoids mechanical forces that could otherwise affect the integrity of the machined components.
The high-quality finish achieved with sinker EDM machining results from multiple passes of the electrode over the workpiece. Initially, a rough cut is performed at high speed, followed by two to three finishing passes that create a mirror-like finish unmatched by other machining methods.
Sinker EDM is distinguished by its unique finish, which features a random texture rather than the directional patterns typical of conventional cutting methods. This exceptional finish is achieved through repeated passes, a technique exclusive to sinker EDM due to its non-contact nature, which avoids the stress and marks that can result from traditional tooling.
The superior surface finish produced by sinker EDM often eliminates the need for further finishing operations. This is particularly important for applications where components must smoothly interact with each other. The non-contact nature of the electrode ensures that the workpiece's surface remains free from cuts or abrasions, preserving its quality throughout the process.
Despite the higher costs associated with sinker EDM machining, it is invaluable for producing complex and intricate designs with exceptional precision. The method excels in replicating computer-generated models with remarkable detail, achieving tolerances as tight as 0.0001 inches (0.00254 mm)—a level of accuracy unattainable with other machining processes.
Sinker EDM is particularly effective for creating blind holes and cavities in irregular shapes, thanks to its ability to use tools precisely shaped like the cavities themselves. It also allows for drilling holes at acute angles to the surface, a capability that conventional machining methods cannot achieve.
This versatility makes sinker EDM the process of choice for high-precision applications involving complex geometries and intricate details. It offers engineers and designers the flexibility to innovate and produce high-performance products with both accuracy and efficiency.
Since its inception, sinker EDM technology has become an essential tool for designers and engineers across various industries. It has proven particularly valuable in the aerospace sector, where precision and meticulous shaping of parts are critical. Similarly, in the medical industry, where errors or flaws in medical devices can have serious consequences, sinker EDM's ability to produce highly accurate and finely detailed components is crucial.
In a case study conducted by a prominent aerospace component manufacturer, sinker EDM was employed to create crucial components for jet engines. This technology enabled the manufacturer to produce complex parts with stringent tolerances and exceptional precision, leading to enhanced performance and reliability of the final product. Furthermore, sinker EDM helped reduce lead times and lower costs compared to traditional machining methods.
In a case study by a medical implant manufacturer, sinker EDM was utilized to fabricate orthopedic implants from titanium. The technology enabled the production of complex, precise designs, enhancing the fit and effectiveness of the implants, and leading to better patient outcomes. Moreover, sinker EDM contributed to reductions in both production time and costs compared to conventional machining methods.
In a case study by an electronics component manufacturer, sinker EDM was employed to create components for microelectronics. This approach enabled the production of tiny, intricate parts with exceptional precision, enhancing the performance and reliability of the final products. Additionally, sinker EDM helped the manufacturer cut lead times and reduce costs compared to traditional machining methods.
In a case study by a tool and die manufacturer, sinker EDM was utilized to create complex dies for stamping operations. The process allowed for the production of detailed designs with exceptional precision, leading to extended tool life and lower maintenance costs. Furthermore, sinker EDM enabled the manufacturer to reduce both the time and expenses typically associated with traditional machining methods.
In a case study by an automotive component manufacturer, sinker EDM was employed to fabricate gears for high-performance applications. This technology enabled the production of intricate gears with precise tolerances, enhancing both the performance and durability of the final product. Additionally, sinker EDM helped the manufacturer shorten lead times and lower costs compared to traditional machining methods.
Sinker EDM machining excels in creating highly precise components from conductive materials. Since its inception, an increasing number of manufacturers have recognized the benefits of sinker EDM for its exceptional accuracy and ability to produce a diverse range of intricate parts.
Sinker EDM is widely used in the manufacturing of molds and dies for injection molding and stamping. The process allows for the creation of complex shapes with high precision and repeatability, which is essential for producing high-quality molded and stamped parts. Additionally, Sinker EDM can be used to create molds and dies from hard-to-machine materials, such as titanium and Inconel, which are often required for demanding applications.
Sinker EDM is widely utilized in the aerospace and defense sectors for manufacturing essential components like jet engine parts, missile components, and other critical applications. The process is well-suited for crafting complex, high-precision components with stringent tolerances, including turbine blades, compressor vanes, and fuel nozzles. Additionally, sinker EDM is capable of working with exotic materials, such as nickel-based alloys, frequently employed in these industries.
Sinker EDM is employed in the medical device industry for crafting surgical instruments and implants. This process enables the production of tiny, complex components with exceptional precision and consistency, crucial for high-quality medical devices. Additionally, sinker EDM is capable of working with biocompatible materials, such as titanium, which are frequently used in medical applications.
In the automotive sector, sinker EDM is utilized to manufacture components like gears, crankshafts, and other intricate parts. This process enables the production of complex, high-precision components with stringent tolerances, which is crucial for high-performance automotive applications. Furthermore, sinker EDM is effective for working with hard-to-machine materials, such as hardened steel and titanium, which are often necessary for demanding automotive requirements.
In the electronics industry, sinker EDM is employed to manufacture components for circuit boards and other intricate applications. The process is ideal for producing small, detailed parts with high precision and repeatability, crucial for high-quality electronic components. Moreover, sinker EDM can work with a variety of materials, including copper, tungsten, and molybdenum, which are frequently used in electronics manufacturing.
Sinker EDM is widely utilized in tool and die manufacturing for its ability to create complex shapes with exceptional precision and repeatability. This capability is crucial for producing high-quality tools and dies. Furthermore, sinker EDM can handle a variety of materials, including hardened steel, which is often necessary for demanding tool and die applications.
Sinker EDM is employed in jewelry manufacturing to create intricate designs and patterns with high precision. The process is essential for producing detailed and high-quality jewelry pieces. Additionally, sinker EDM can work with a variety of materials, including precious metals and gemstones, which are commonly used in the jewelry industry.
Sinker EDM is also utilized in the production of consumer products, including eyeglass frames, watches, and writing instruments. The process excels in creating small, intricate parts with high precision and repeatability, crucial for producing high-quality consumer items. Furthermore, sinker EDM can work with various materials such as stainless steel, aluminum, and plastic, which are commonly used in the manufacture of these products.
Despite its numerous advantages, sinker EDM does have limitations. The process is relatively slow and not suited for high-volume production, making it less ideal for applications requiring rapid manufacturing. Additionally, sinker EDM machines are expensive to purchase and maintain. While the process offers exceptional accuracy and precision, these drawbacks necessitate careful consideration when deciding whether to use sinker EDM for a given application.
The recast layer forms when molten metal from the EDM cutting process cools and solidifies on the surface of the workpiece, contaminating it. This layer, which contains metal globules and electrode particles, alters the metallurgical structure of the part. The recast layer is a byproduct of the EDM process and can affect the quality of the finished workpiece.
The recast layer induces tensile stress in the part, which can lead to cracks. To ensure the quality and integrity of the workpiece, various processes are employed to remove this recast layer.
The low material removal rate is a notable disadvantage of the sinker EDM process, which engineers are actively working to address. Unlike conventional machining methods that quickly remove surface material, sinker EDM relies on a slow sparking process to erode particles from the workpiece. This slow material removal can be time-consuming and adds to the cost of the final product. What might be accomplished in minutes with conventional machining can take significantly longer with sinker EDM, affecting turnaround times and on-time deliveries.
In sinker EDM, the electrode, which is shaped like the final product, is slowly pressed into the workpiece. This slow process is necessitated by the fact that the electrode does not come into direct contact with the workpiece. Instead, it generates sparks that erode material in a controlled manner, making the production process more time-consuming compared to conventional methods.
The selection of materials for sinker EDM machining is limited to those that are electrically conductive, such as metals. This restriction excludes materials like plastics, ceramics, and other non-conductive substances, thereby limiting the range of products and parts that can be produced. As modern manufacturing increasingly utilizes heavy-duty plastics for various applications—due to their cost-effectiveness and flexibility—sinker EDM's application is confined to scenarios where conductive metals are necessary.
Sinker EDM is particularly suited for producing precision components required for heavy-use applications where the unique properties of conductive metals are essential. However, these metals are costly and the machining process is time-consuming. Manufacturers must weigh these factors carefully when choosing the appropriate machining process for their needs.
The initial cost of using sinker EDM as a machining method is largely associated with the production of the tool or die used to create a part or component. This expense arises because the dies are often made from high-quality materials like graphite, copper, or tungsten, which are machined with exceptional precision to ensure compatibility with the sinker EDM process. For achieving finer surface finishes, additional roughing and finishing tools are required, further increasing the cost.
Sinker EDM is specifically used for producing complex and intricate designs, necessitating highly precise dies and tooling. The conductive metals used in sinker EDM are robust and designed to withstand the machining process as well as the final application. As a result, only larger machining organizations with the resources to afford these high costs typically undertake sinker EDM projects. The combined expenses of tooling, time, and process complexity make the decision to use sinker EDM for part production a critical one.
The sinker EDM process poses several hazards due to its production of toxic emissions, debris, and electrode materials, which are challenging to recycle and degrade. During the erosion process, sinker EDM generates smoke and fumes whose composition depends on the type and viscosity of the dielectric fluid used. Synthetic dielectric fluids, for instance, produce aliphatic hydrocarbons, aerosols, and benzene, all of which are harmful.
Sinker EDM involves a reaction between the workpiece and the electrode, leading to environmental and health risks. The process releases toxic materials that can damage the environment and pose health risks to workers. This aspect is a significant consideration when choosing sinker EDM as a manufacturing method.
In addition to gas emissions, volatile particles from the workpiece are released into the air and can cool to form dangerous carcinogenic substances. To mitigate these risks, it is essential to submerge the workpiece at a specified depth in the dielectric fluid to prevent particles from escaping into the atmosphere. Moreover, proper filtration and ventilation systems are crucial to capture these harmful particles and maintain a safe work environment.
Despite its precision and advantages, sinker EDM requires careful monitoring and management of these negative factors. Manufacturers must take extensive measures to ensure that their use of sinker EDM is safe for both the environment and their employees.
EDM machining is a contemporary machining method based on the removal of material from a part using thermal energy. The material is removed by local melting or vaporizing small areas on the surface of the part being machined...
A method of precision machining called electrical discharge machining (EDM) removes material from a workpiece using thermal energy rather than mechanical force. A thin, single-strand metal wire and deionized water used to...
The normal functioning of CNC machines is done along the three Z, X, and Y axes. The five axes machines have two more axes accessible, which are namely A and B. The addition of the two extra axes makes it easy to cut complex and intricate parts...
CNC machining is an electromechanical process that manipulates tools around three to five axes, with high precision and accuracy, cutting away excess material to produce parts and components. The initial designs to be machined by CNC machining are created in CAD...
The CNC process was developed in the 1950‘s and took a leap forward in the 1980‘s with the addition of computerization. Unlike other production processes, CNC begins with a rendering by a computer, which creates a two or three dimensional representation of the part to be produced...
G-code is the name of a plain text language that is used to guide and direct CNC machines. For most modern CNC machines, it isn‘t necessary to know the meaning of G-codes since CAD and CAM software is translated into G or M codes to instruct a CNC machine on how to complete a process...
Computer numerical control (CNC) is a fundamental part of modern manufacturing. The majority of machines operate using instructions and guidelines that have been downloaded using a CNC program controller...
Water jet cutting is a manufacturing process that uses high pressure jets of water provided by pressurizing pumps that deliver a supersonic stream of water to cut and shape various types of materials. The water in water jet cutting is...
Machining is a manufacturing process used to produce products, parts, and designs by removing layers from a workpiece. There are several types of machining that include the use of a power driven set of machining tools to chip, cut, and grind to alter a workpiece to meet specific requirements...
The CNC process, computer numerical control, is a method of manufacturing where programmed software directs the operation of factory tools and machinery. It is designed to manage a wide range of complex machines from grinders and lathes to mills and routers...